Hydrogen:
Metallurgical purification without emissions
In a pilot project at the Hamburg plant, Aurubis successfully tested the use of hydrogen in the anode furnace. This facilitates a reduction process without CO2 emissions.
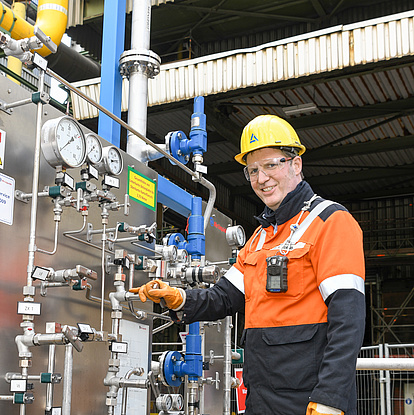
Successful pilot project
Aurubis was the first company in the copper industry to test the use of hydrogen on an industrial scale. In a pilot trial extending over several weeks at the Hamburg plant, we used a gaseous mixture of hydrogen and nitrogen in place of natural gas to pole copper melt in the anode furnace during production. Poling refers to a metallurgical purification process or a reduction process in melted metal. When feeding in the gas mixture, excess oxygen bound to the copper is drawn out of the copper melt.
In the current process using natural gas as a reducing agent, carbon dioxide (CO2) is formed as a by-product. These CO2 emissions can be avoided when a gas mixture is used in reduction – in this case, water vapor is the only by-product of poling. A regulating station plays a crucial role in this pilot process, keeping the pressure in the anode furnace constant through the feed nozzles. Factsheet Hydrogen
The foundation for a future with hydrogen
This project enabled us to test the reaction of the facilities to the hydrogen fed into them, and we were able to get this production step up and running smoothly. As a result, Aurubis has laid the foundation for additional Group activities with hydrogen thanks to the technical experience gathered in the pilot.

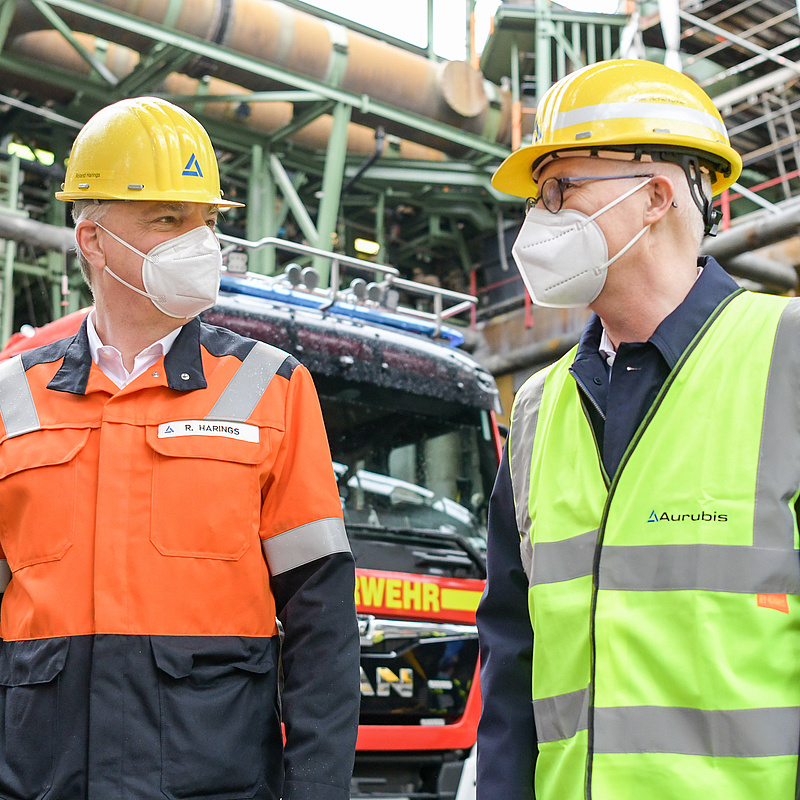
“With the successful launch of the hydrogen pilots, Aurubis visualizes a carbon-neutral future with the help of innovation.”
— Roland Harings, CEO