PIP and CI:
From the idea to the improvement
Aurubis is always on the lookout for process improvements, whether in production or along the supply chain. In doing so, digital solutions play a pivotal role.
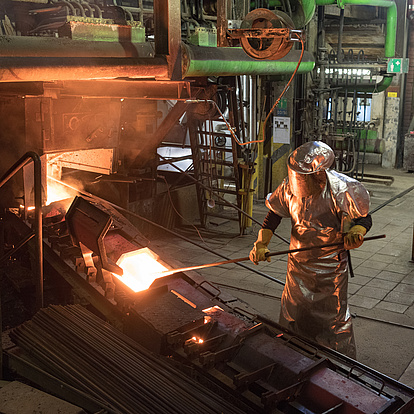
>350
Ideas for improvements are currently being implemented in concrete projects
There’s a lot going on at Aurubis: through the Performance Improvement Program (PIP), the company is permanently reducing its costs and boosting its performance. We will achieve the full impact of € 100 million on earnings by fiscal year 2022/23. At the moment, we’re gradually implementing more than 350 improvement ideas within the context of PIP, including a project to increase throughput in the Hamburg primary smelter Rohhütte Werk Ost (RWO).
PIP focuses on sales, administrative, and overhead costs, (non-metals) procurement at Group level, and production and maintenance in Hamburg. At the same time, the new corporate function Continuous Improvement (CI) zeroes in on cross-site improvement of production processes with the help of the Aurubis Operating System (AOS) and digital tools. For this purpose, the Digital Factory program was started as an overarching initiative to improve production processes with data-driven tools under the collaboration of azeti, IT, and CI, among others. azeti is a software company from Berlin that has been part of the Aurubis Group since 2020.
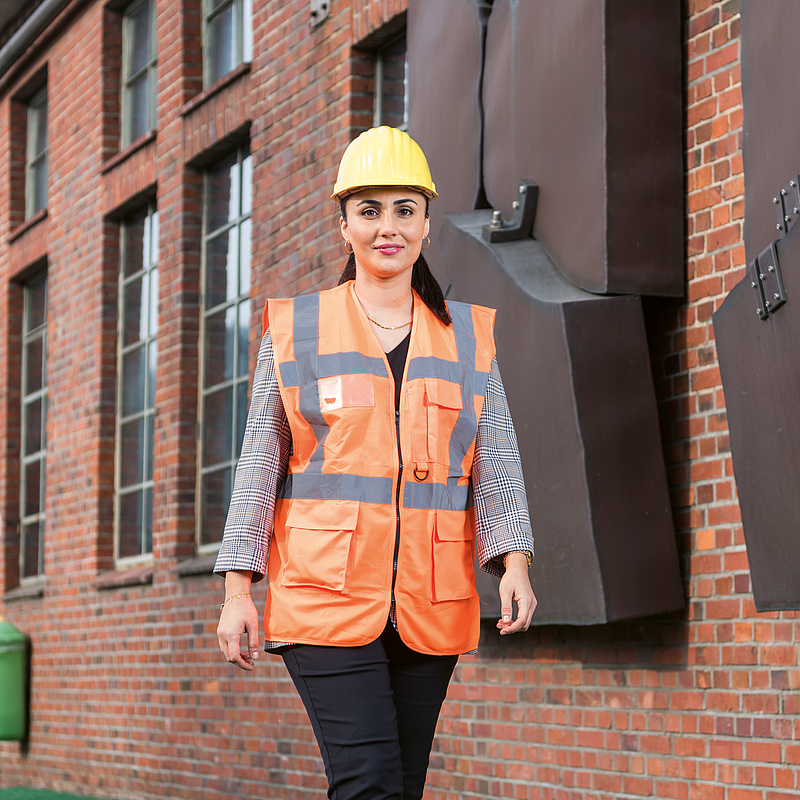
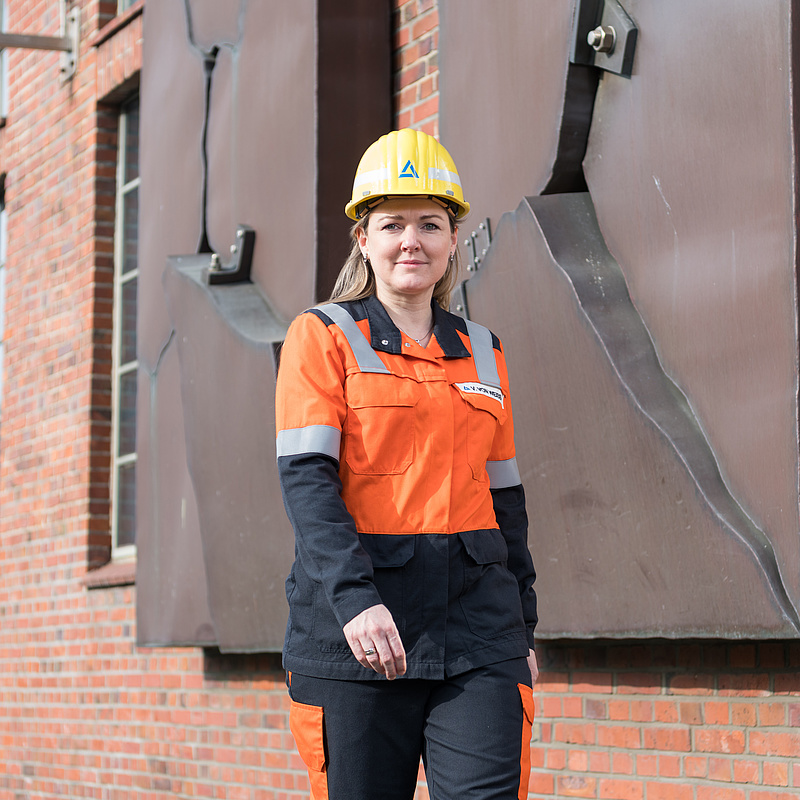
In Hamburg, CI is currently working with colleagues in engineering, IT, and azeti on using the azeti platform on the anode casting wheel and the flash smelting furnace, for instance. The IoT (internet of things) platform is already being tested on the anode casting wheel to monitor the production process in order to detect and remedy disruptions early on. This is referred to as predictive maintenance. At the flash smelting furnace, the software is being used in a project to optimize combustion.
The projects of the Digital Factory program always serve the purpose of supporting colleagues in the plants with their work and enhancing plant availability. This is also true for a project that will require more of CI’s energy in the coming weeks and months: harmonizing maintenance processes across the Group.
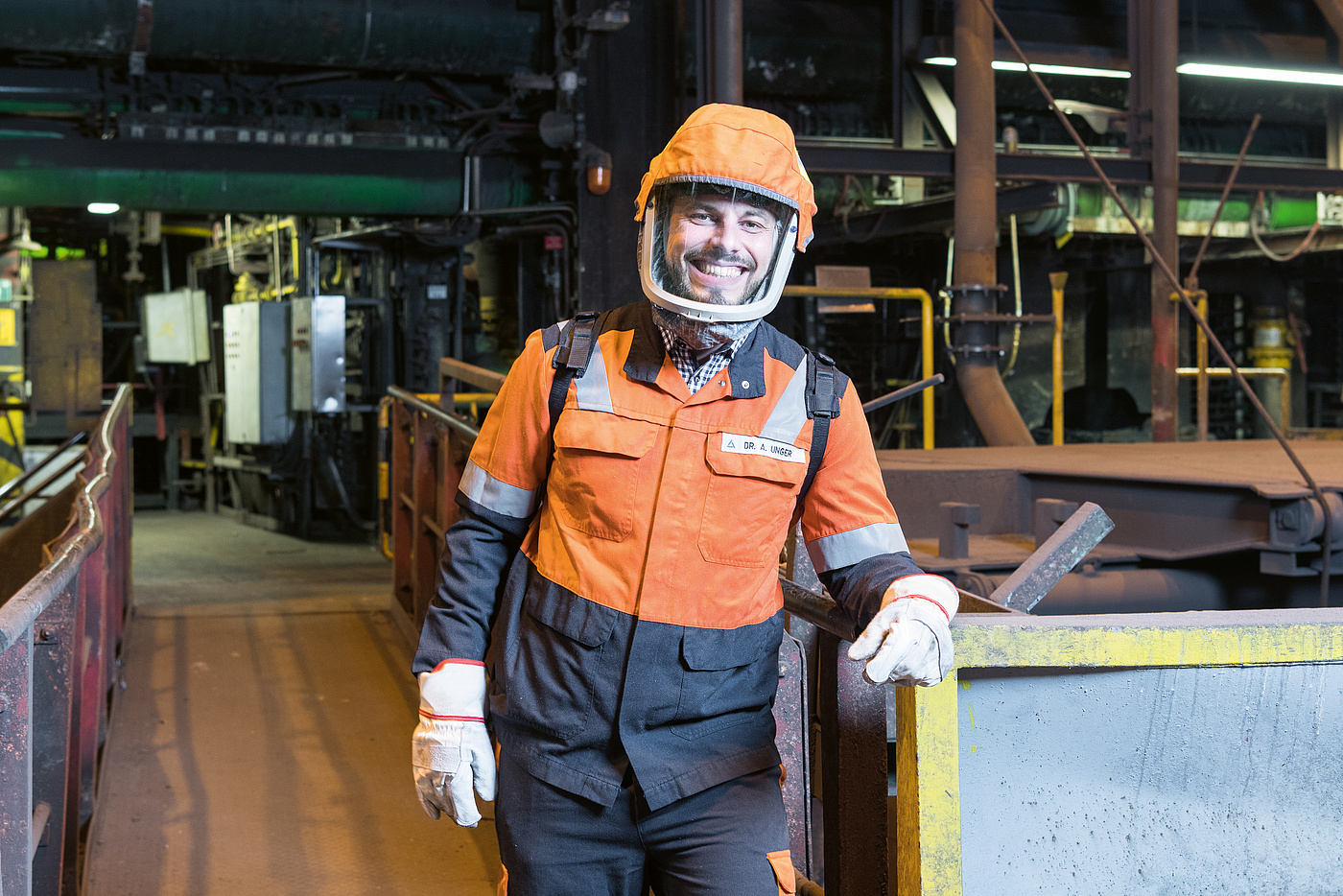
For maximum concentrate throughput in our flash smelting furnace, the combustion of the copper concentrate has to be consistent. The temperature is monitored at over 180 temperature recording points on the reaction shaft for this purpose. In the case of consistent combustion, the temperature is the same everywhere. If the temperatures are different, the center lance has to be used to check whether the concentrate is being directed into the furnace on one side. In this case, the furnace has to be stopped for 15 to 20 minutes and the nearly 5 m long, 400 kg heavy center lance is removed. The azeti software was introduced to the process at the Hamburg site to optimize combustion and avoid unplanned center lance inspections. It conveys the relevant process, temperature, pressure, and volume data to the control room employee that they can use at any time to manage things in a targeted way. In the second stage, they should then also be shown additional parameters to be able to optimally operate the flash smelting furnace. Production, engineering, azeti, IT, and the Analytics Center of Excellence work together on the Digital Factory project team for this project. The azeti platform gathers all of the data necessary to monitor and visualize the process. The Data Science Team from the Analytics Center of Excellence is responsible for analyses and model calculations.
On the basis of more than 20 workshops with suppliers, customers, and internal stakeholders, Aurubis developed ideas for a digital business partner portal and defined its requirements. This includes fixing contractual volumes or calling up contract data from the previous Copper Online platform. We’re currently subjecting the first product entities to a practical test in a trial phase with customers and suppliers. Projects like this are making the management of our production network leaner, more digital, and even stronger.
One objective of PIP is to increase concentrate throughput in the Hamburg plant’s primary smelter Rohhütte Werk Ost (RWO). To that end, a team set about figuring out how the regular partial repairs and relinings of the converters could be carried out in a shorter period of time – with the goal of enabling the smelter to run in three-converter operation for longer. The result: technical upgrades, standardized processes, and modified work hours have reduced repair times by six days. Six days in which we can produce more.
Aurubis doesn’t just rely on digital solutions in production. We want to work together more digitally with our customers, too, providing them with added value. We established the InnoLab in September 2020 with this purpose. There, we develop digital services and solutions that enhance our products’ appeal and strengthen customer loyalty.